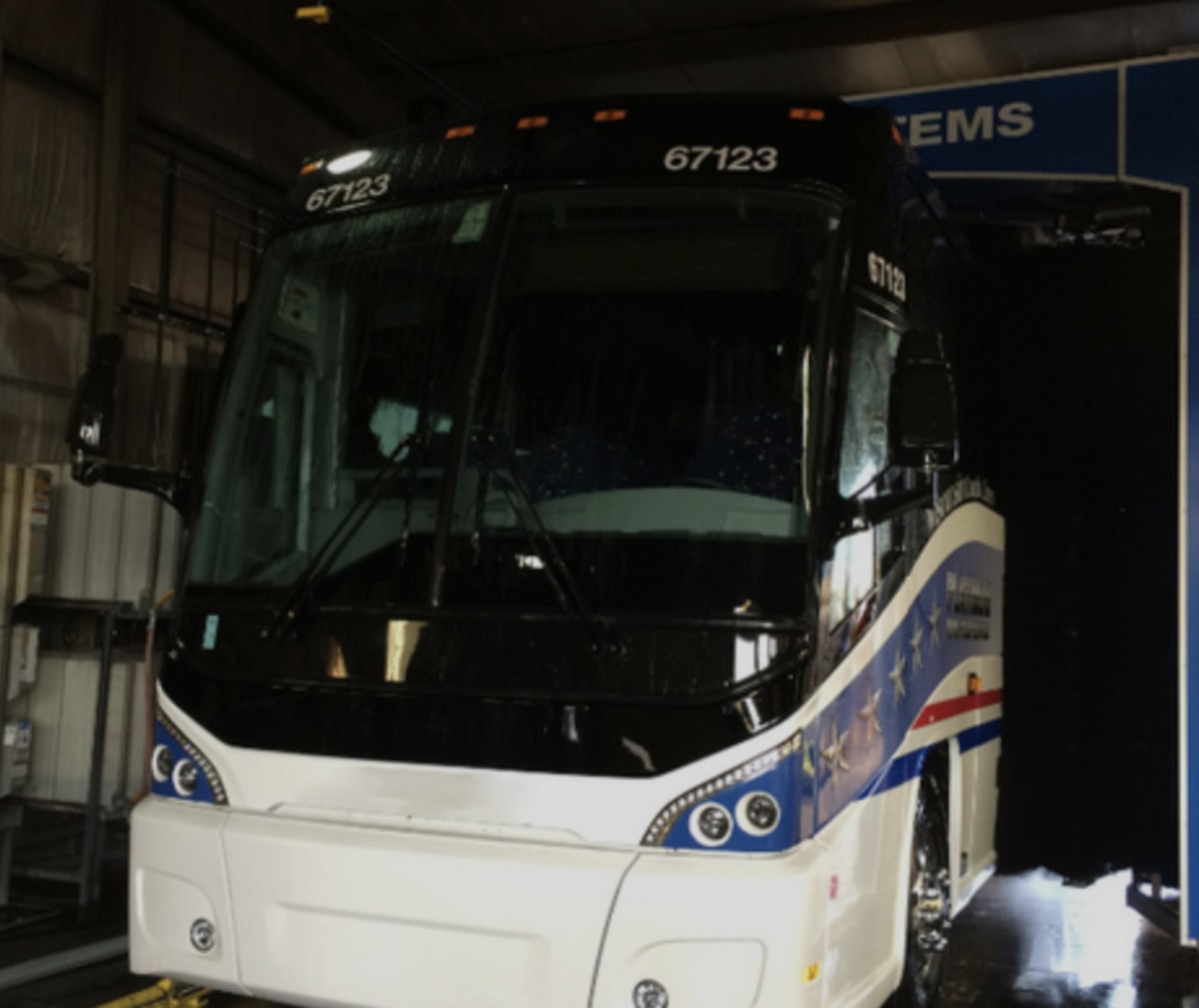
What to Look For When You Upgrade Your Bus Wash Systems
For Public Transit Authorities
January 15, 2022
The demand for high efficiency bus wash systems is on the rise and public transit authorities are looking for more efficient and sustainable ways to manage their vehicle maintenance needs. Whether you have a fleet of 20 vehicles, or hundreds, what your vehicle looks like says a lot about you and your operation. Keeping transportation fleets clean and polished is key to a successful Public Transit Authority.
Sustainable Bus Wash Systems for Public Transit Authorities
We spoke to key Public Transit Authorities to get the top 5 things to look for in a wash system. Wash system manufacturer Whiting Systems created a list to keep handy during the bid process for a bus or passenger rail wash system. We’ll help you determine the top component you should consider when putting in a bus wash system or passenger rail wash system, especially for cities with a focus on green options and high efficiency systems. Public Transit Authorities trust Whiting Systems to provide sustainable wash programs for public transit buses and rail systems.
The five main components Public Transit Authorities should considering during their upgrade progress are:
- Wash quality
- Wash times
- Operating and lifecycle costs
- Technology developments
- Green choices
- Manufacturer quality and track record
System Wash Quality
A quality wash promotes a strong image while communicating safety to the public. Public Transit Authorities should prioritize the quality of brush materials and styles for the best result. Some manufacturers have turned to using foam materials in brushes. Instead, Whiting Systems Wash uses turning soft synthetic fiber in their Smart Brush Technology to polish the vehicle and reach the harder corners and turns on the vehicle.
“Whiting Systems Smart Brush Technology is one of a kind in the world as it senses pressure points while washing the vehicle. Several Transit Authorities choose the Whiting Brush system because of the longevity over others,” shares Rush Whiting of Whiting Systems.
To thoroughly clean the dirtiest parts of the vehicle — the front and back —Whiting Systems high efficiency systems employ brushes that cradle the vehicle on the sides, front, top, and back.
We help our transit authority partners cut down on their water usage and power over older traditional machines by 90%.
System Wash Times
Improving wash times helps Public Transit Authorities keep rolling washes frequently without interruption to other necessary yard processes. Depending on the number of vehicles in your fleet, some wash system types are better suited for a particular fleet. Whiting Systems helps you determine what kind of system is best for you.
Typically, transportation operations with fleets of more than 50 vehicles install a drive-through type system, where a bus drives through a series of brushes and rinses. Railway wash systems are customized to rail system needs.
Smaller fleets tend to use a gantry system, where a vehicle is stopped and the wash system rides on a track while it washes the vehicle.
“One of the big advantages of the gantry system is you can wash all types of vehicles,” says Greg Jenkins, Vice President for Whiting Systems.
The specifications of your transportation fleet depend on exactly what type of system you need.
John Criscuolo, account manager at Whiting Systems adds, “Gantry designs incorporate high-speed PLC (programmable logic controllers), an industrially hardened computer, which manages an array of functions including imaging the vehicle, managing brush contact pressures, gantry speed and application points for cleaning products.”
Bus Wash System Operating and Lifecycle Costs
One of the highest impact factors for a public transit authority is operating and lifecycle costs of bus wash systems. Public transit authorities consider efficiencies of systems including whether the wash system uses less water and electricity. This has a considerable long term impact on the viability of your bus wash system. Operating and lifecycle costs have three subparts: durability, infrastructure and warranties.
Wash System Durability
Public transit authorities require frequent, nightly bus washes. Can your bus wash system withstand high usage over time? Whiting Systems focuses on maintaining the long term value of your wash system. With simplicity of design and attention to details, Whiting Systems is able to lower maintenance costs.
Infrastructure for Your Wash System
Public transit authorities need to know if their existing utilities — water, air, electricity and drainage — will support a heavy-duty wash system. They must also consider the space that will contain the wash system. By partnering with an expert at Whiting Systems, we can tailor your wash system to meet your existing infrastructure.
Bus Wash System Warranties
Is the wash system covered by a manufacturer’s warranty? Typically, warranties for components are one year, while coverage for structures is 10 years to 15 years. In addition to Whiting Systems standard warranties, we are known for exceptional preventative maintenance and the fastest response time for wash system issues. Our service team is constantly monitoring your wash system in real time to protect you from problems and service errors. Whiting’s after sale customer service is the only one of it’s kind and they even service most of their competitors units that have failed.
Wash System Technology Developments
Wash system technology has improved dramatically with Whiting System innovations.
“New developments in vehicle washing systems include the use of electronically controlled brushes, which helps reduce maintenance costs,” says Greg Jenkins, Vice President of Whiting Systems.
Other innovations include the ability for manufacturers to remotely monitor the wash system via the Internet, providing data on washes and diagnosing any issues.
“We have the ability to remotely monitor and diagnose problems and upgrade the wash system programs. This allows us to make custom changes to system” processes from our offsite Command Center,” Criscuolo says. “We can provide information on each wash performed. Reports are available via private website access or email.”
Green Choices for Wash Systems
In an effort to reduce environmental impacts, as well as cut down on water costs, Whiting Systems has developed water and power saving technologies. These are fast becoming standard features on vehicle wash systems. Whiting Systems HE High Efficiency Scout reduces water and kilowatt usages. We see older competitive wash systems using as much as $2.00 in energy and water. Whiting Systems High Efficiency Scout runs a wash cycle at close to .25 cents. We have a 70%-90 % reduction in that cost being more sustainable for years to come.
Some recycling systems can reclaim as much as 85% of the water.
The remaining wastewater that is not recycled is filtered through the company’s patented water purification system. Through this chemical-free process, wastewater can reach a purification level of 99% — now clean and safe to proceed out into the sewage system.
“A well maintained reclaim system will return quality re-use water to the wash system,” Criscuolo says.
“This is a requisite for a quality wash process. It is essential that end users understand the balance between wash water reclaim, required maintenance and the wash process,” he adds.
Another green aspect of the wash system is the use of enzyme-based vehicle wash agents.
Sustainability has also extended into the manufacturing process, as some wash systems are built with eco-friendly materials. Whiting Systems use all stainless steel in our fabricating, because it doesn’t rot away like other metals and is recyclable.
Manufacturer Quality and Track Records for Bus Wash Systems
Transit managers need to look beyond the wash equipment and consider the company’s track record, service, warranty, and beyond the sale. We see many competitor systems now that are 3, 5, or 8 years old that the transit manager cannot get service or parts for. Whiting Systems suggests you talk to many references in the transit arena to see exactly who is servicing and who is not. We encourage public transit authorities to visit the manufacturer.
“A plant validation tour is encouraged, as it reveals much about the prospective vendor. Customers are also encouraged to ask about programs after the sale like maintenance services,” says Criscuolo.
Speaking to previous clients is also recommended so prospective buyers can get unbiased opinion on products. Always ask for references and do your due diligence with these questions above. Transit authorities procurement officers now know cost is not what they should hang their hat on. They have turned to value, efficiencies, service contracts, parts availability, after sales customer service, account management, availability and time frame.